High-speed stamping die cleaning process, die oil cleaning
I. Common Types of Dirt on Stamping Dies
1. Oil stains and lubricating residue: Residues of lubricating oil, release agents, etc., used during stamping.
2. Metal debris: Small particles such as aluminum chips and iron chips generated during stamping.
3. Oxide layer and corrosion: Oxide layer formed on the surface of the die after long-term storage or use.
4. Adhesive residue: Residues of sealants or adhesives used in some processes.
II. Cleaning Process Flow (Detailed Step-by-Step Explanation)
1. Pre-treatment stage: Initial manual cleaning: Use soft brushes, air guns, or vacuum equipment to remove large debris and loose dirt from the surface of the die.
Degreasing treatment: Spray environmentally friendly degreasing agents on areas with serious oil stains to soften stubborn oil stains.
2. Main cleaning stage
High-pressure water cleaning
Equipment: Industrial-grade high-pressure cleaning machine (pressure range 50-150 MPa, adjustable temperature).
Process: Use a fan-shaped nozzle to rinse the die grooves, holes, and other complex structures with 60°-80℃ hot water and neutral cleaning agent.
Advantages: Efficiently removes oil stains and debris, avoiding damage to the die surface.
Ultrasonic cleaning (optional)
Applicable scenarios: Precision dies or deep hole/blind hole structures.
Process: Immerse the die in an ultrasonic tank to peel off micron-level residues through high-frequency vibration, and use special cleaning agents to improve the effect.
3. Post-treatment stage
Rinsing and drying
- Rinse the surface of the die with deionized water or pure water to avoid scale residue.
- Dry with compressed air or low-temperature drying oven (temperature ≤ 80℃) to ensure the die is completely dry.
Rust prevention treatment
- Spray water-based rust inhibitors or perform short-term oil sealing to prevent oxidation during storage.
III. Cleaning Quality Inspection Standards
1. Visual inspection: No visible oil stains, debris, or water stains on the surface of the die.
2. White glove test: Wipe the surface of the die with a clean white cloth, no black stains.
3. Functionality verification: After cleaning, assemble the die for test stamping to ensure that the stamped parts have no scratches, indentations, or other defects.
IV. Safety and Environmental Protection Requirements
1. Operational safety
- Wear protective equipment (goggles, gloves) for high-pressure equipment.
- Set warning signs during high-temperature cleaning to avoid burns.
2. Environmental protection measures
- Cleaning wastewater needs professional treatment to meet discharge standards.
- Prioritize biodegradable cleaning agents to reduce environmental pollution.
V. Equipment Recommendations and Process Optimization Suggestions
1. Adaptable equipment
- High-pressure cleaning machine (recommended pressure 100 MPa or higher, with heating function).
- Multi-tank ultrasonic cleaning line (for small and precise dies).
2. Process optimization
- Adjust the pH value of the cleaning agent according to the die material (such as steel, aluminum) to avoid corrosion.
- Regularly maintain cleaning equipment to ensure pressure and temperature stability.
VI. Service Promise
We can provide customized cleaning solutions and equipment configurations according to customer die types, dirt characteristics, and production capacity needs, and provide process guidance and Powered by throughout the process to ensure cleaning efficiency and die service life.
Note: This document is a general technical description. Specific process parameters need to be adjusted according to the actual working conditions.
For further consultation, please contact our technical team to obtain a customized solution!
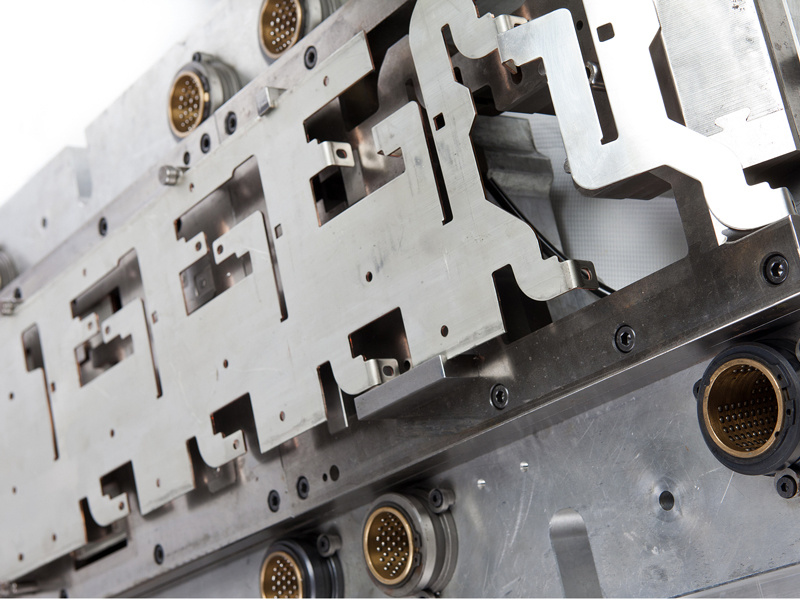
Previous Page
Next Page